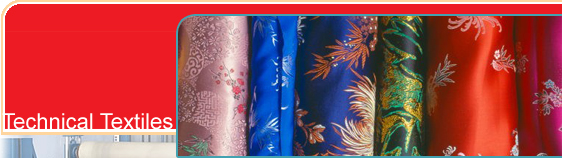
RFL Dipping Plants
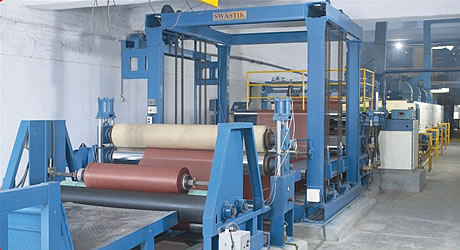
RFL dipped fabrics are the backbone of high quality rubber products like tyres, conveyor belts, diaphragms, floats etc. For different applications and different fabrics, the lines can be designed as dip – Stretch lines or Stretch – dip lines or a combination of both. For heavier fabrics, the line could be double dip – stretch Line.
Dipping Lines are generally put together using the following individual components.
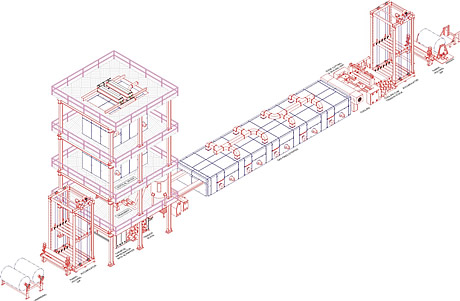
Unwinder / Let-Off
Fixed dual stations or Turret type unwinders with brakes or AC vector drive for tension control. Closed loop control with load cell feedback provide required tension to process both light and heavy fabrics.
Accumulators
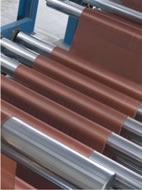
Accumulators
In varying capacities using hydraulic cylinders or variable speed AC motor to meet speed requirements.
Dipping Stations
Low liquor Dip Tanks, sized to minimize dip solution waste and equipped with Hi-Squeeze Rolls to ensure uniform squeeze pressure across the web width.
High-Speed Back-to-Back Double Dipping System
Back to back dipping system can be provided to treat heavier Nylon, and Polyester tire cord fabrics and multiple process specifications suitable for higher speeds over 80 mpm. Squeegee
Adjustable Stainless Steel doctor blades, one on each side of the fabric.
Suction Extractor / De-Webber
Includes a vacuum head on each side of the web fixed on adjustable slides, a primary separator box, a secondary separator, a bag filter and fan. Vacuum pressure is controlled using inverter AC variable speed drives with feedback pressure sensors. Precision machined nozzle slots ensure accurate suction velocity.
Tension Stacks and Cooling Rollers
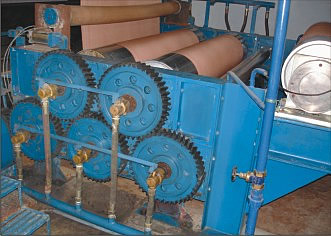
Perfectly Matched machining and grinding for perfect alignment of rolls, bearings and gears. Each tension stack can be equipped with an automatic lubrication system for the gears. The number and size of tension stack rollers and bearing is determined by load requirements. Double shell cooling rolls are provided to cool the web after the oven with the cooling water moving in a spiral between the two walls. For machines with lower production requirements or for lighter fabrics the cooling rollers can be combined with tensioning rollers.
Drying & Heat Setting Chambers
A series of vertical dryers heated by direct fired modulating gas burners, supplied for use with sulphur free Natural Gas. Can be precisely controlled to obtain drying and heat setting temperatures within required tolerance. The radial blowers circulating the air in the treatment chamber are directly coupled to inverter controlled AC motors to obtain the required air velocity. The web passage through the dryer is vertical and the turning rollers are water cooled.
For light belting and chaefer fabrics, the line is equipped with a stenter to impart weft wise stretch to the dipped fabric during the heat setting operations.
Edge Trimmer
Several slitting options offered for edge trim, including trim removal. For Chafer Fabrics, an ultrasonic Fabric sealing device can be provided prior to the fabric slitter.
Wind-up
Turret type or stationary surface windup to match individual process requirements. The precise Surface Winders produce rolls up to 2000 mm diameter and ensures a finished roll with straight edges within a close tolerance.
Drive
The machine is equipped with AC inverter drives having Vector control technology to provide the highest level of accuracy and are controlled by a PLC to maintain speed and tension.
Controls
Defect free fabric needs constant tension and must be perfectly centered and properly guided throughout its run in the machine. Load cells provide closed loop control for tension. Centering arrangements, web aligners and expanders are provided as required by the process and the fabric.
PLC with an HMI monitors and records process information. Controlling these critical and crucial functions via recipe management, SWASTIK RFL Dipping Lines assure consistent process conditions one lot after another, year after year.
The recipe manager automatically sets speed, temperature, tension, and other variables to simplify operations.
The operator interface (HMI) is an easy-to-use, intuitive graphic colour display.
The PLC stores data for historical trending and can print a quality report on request.
Modem communication can be provided for remote diagnosis.
Tension Stacks and Cooling Rollers
1. | DIP – STRETCH WITH VERTICAL DRYER AND STENTER for Chafer and light NN & EP Belting. |
2. | STRETCH – DIP WITH VERTICAL DRYER for Tyre-Cord Warp sheets |
3. | DIP – STRETCH WITH VERTICAL DRYER for NN belting fabrics. |
4. | STRETCH-DIP CUM DIP-STRETCH WITH VERTICAL DRYER for both Warp sheets as well as NN Belting Fabrics. |
5. | DOUBLE–DIP STRETCH STENTER BASED PLANT for EP Belting made of non Adhesive Activated Yarns. |
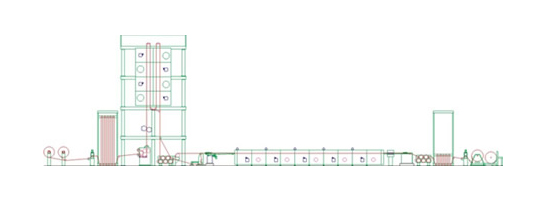
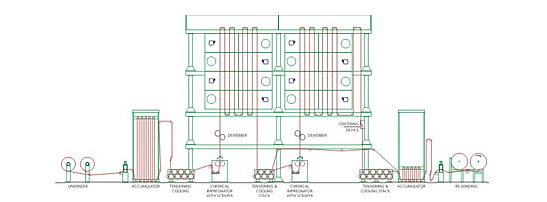
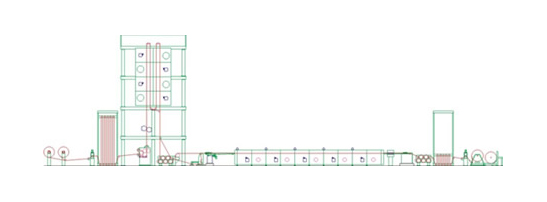